Steps to prevent Corrosion from Steel
What is Corrosion in Steel?
The irreversible deterioration in steel for various environmental factors such as acid, moisture etc. is known as corrosion. Corrosion causes the destruction of the steel material due to chemical reaction or various environmental factors. Steel corrosion involves an electrolysis for which the metallic surface releases electrons into an electrolyte. For moist in air or other factors iron in the steel tend to go back to its original state that is iron oxide or rust.
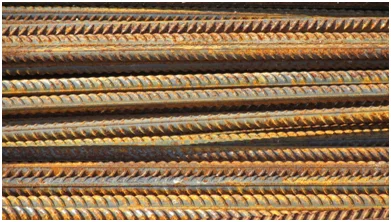

What to be done to prevent Corrosion in Steel TMT Bars?
It cannot be taken lightly. The entire buildings strength depends upon RCC and steel bars are the most important factor to it. For corrosion steel loses its strength therefore the entire structure can be affected. Preventive measure need to be taken in order to avoid corrosion to Steel TMT Bars.
- Avoid heavy reinforcement especially at the intersection of beams and columns
- Try to keep the steel in a distant zone from other construction material such as bricks, wood and other
- Keep the Steel Bars in dry place where it cannot be exposed to rain, snow, salt elements etc.
- It is highly recommended to clean the TMT bars to clean with wire-brush before placing
- Electroplating – Cover the surface of TMT Rebar with a Thin layer of Nickeletallic plating is one of the best ways to prevent corrosion.
- Mechanical Plating – In Steel bar surface zinc or cadmium can be applied to prevent corrosion
- Steel Rebar can be dipped into molten zinc the process is known as Hot Dipping
- Choosing the best quality TMT Rebar that does not have Sulphur & Phosphorus in high ratio. Shyam Steel Fe 500D TMT Rebars has 0.065% Phosphorous + Sulphur that makes it highly resistive to corrosion.
- Use the correct ratio of water-cement is essential
Anti Corrosion Treatment
It is essential to run the alkaline solution in TMT Rebars for the areas that carry high moisture in air for example coastal areas. Certain number of steps needs to be taken for Anti corrosion treatment.
Step 1 – Reinforced bars are submerged in de-rusting solution in about half an hour until the rusts are removed and bright surface of the bars are visible
- De-rusting solution is prepared by mixing
- 50 litres of hydrochloric acid
- 50 litres of Water
- 5 litres of inhibitor
After this the bars should be taken out of the solution and clean with wet cloth
Step 2 – The bars are again submerged to the Alkaline Solution. Alkaline solution is prepared with
- 1 kg of Alkaline Powder
- 400 litres of Water
The bars should be in the solution for 5 minutes then to take out and cleaned.
Step 3 – After the Alkaline Treatment, Phosphate Jelly has to be applied with a fiber brush. The jelly will be taking time around an hour (60 minutes) to react with the bar then to be cleaned with water
Step 4 – In next step Corrosion Inhibitor Solution to be applied to the bars by fiber brush/dipping
- Corrosion Inhibitor Solution is made with
- 500 CC of inhibitor
- 1 kg of Ordinary Portland Cement
This semi liquid mixture is applied to the rods surface with fiber brush. The mixture should be applied on the same day it is prepared and it is allowed to be dry for a day. It needs to be dried on rod surface completely
Step 5 – Then finally the Corrosion Sealing Solution needs to be applied to the rods surface. It approximately takes 4-5 hours to dry on air completely. Once it is dried completely it needs to be repeated once again.
High Quality Corrosion Resistant TMT Rebar
Globally Corrosion resistant tmt rebars are high in demand across varied industries. This is essentially for three major elements
– Improved strength
– Improved Ductility
– Anti Corrosion Properties
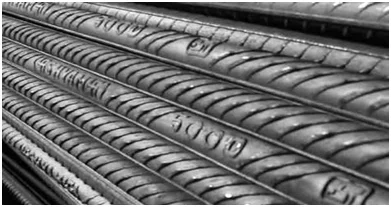
High Quality Corrosion Resistant (CRS) TMT Rebars are evaluated and tested with various and rigorous corrosion media as per ASTM Standards (American Society for Testing and Materials). These tests include
- Alternate Immersion Test
- Salt Spray Test
- Sulphur Dioxide Test
- Potentio Dynamic Test
According to the result Shyam Steel’s Corrosion Resistant TMT Rebars (CRS) are more corrosion resistant than any other TMT Rebars.
Type of Test | Non CRS TMT Rebars | Corrosion Resistant TMT Rebars (CRS) |
Alternate Immersion Test | 1.0 | 1.92 |
Salt Spray Test | 1.0 | 1.59 |
Sulphur Dioxide Test | 1.0 | 1.68 |
Potentio Dynamic Test | 1.0 | 2.35 |
The idea was to make you understand how important it is to take care of the corrosion from TMT Steel Bars. It can be fatal if corrosion in TMT Bar you treat lightly. Therefore, while constructing only choose the CRS/Corrosion Resistant TMT Rebars only.