Shyam Steel has best quality steel manufacturing Integrated Steel Plants located in West Bengal. Our state-of-the-art Integrated steel plant includes manufacturing setup like DRI Unit, EAF, Continuous Billet Casting Mill, sophisticated and high-speed Rolling Mill, microprocessor-based product technologies and fully-equipped Quality Assurance & Testing laboratories. Our Best Quality TMT Bar is most preferred for all type of construction purposes across India.
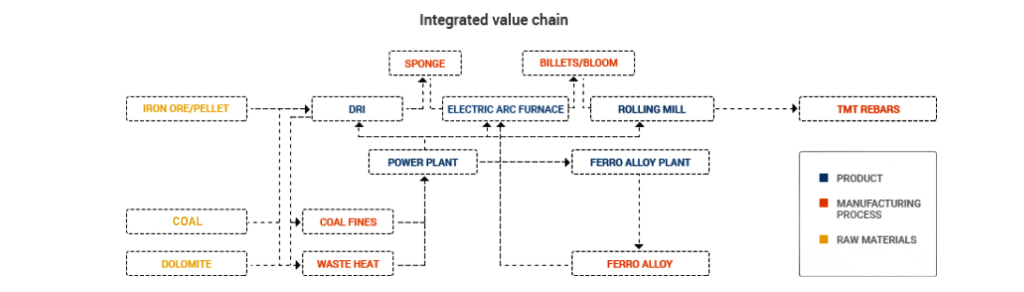
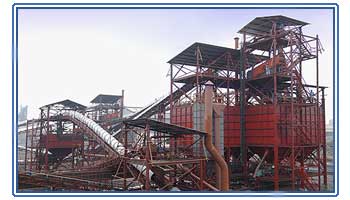
Shyam Steel’s Durgapur Unit is an automated integrated steel plant comprising
- DRI Unit
- Steel Melting Shop Equipped with Electric Arc Furnace
- Continuous Billet Casting Unit
- Rolling Mill with Thermex System
It has been set up in collaboration with World-renowned companies viz; Concast AG-Zurich and HSE Germany.
DRI Unit
Best TMT Bar Manufacturing Plants India – In the Direct Reduced Iron (DRI) plant, production of sponge iron using a solid reductant involves reducing iron ore (lumps/pellets) with a carbonaceous material such as coal. The reduction is carried out in a rotary kiln (which is inclined and rotates at a predetermined range of speeds) at a stipulated temperature (8500C – 10500C). The inclination and the rotary motion of the kiln ensure that the raw materials move from the feed end to the discharge end of the kiln and during this movement the actual reduction of iron ore to iron takes place. The material discharged from the kiln is taken to a rotary cooler for cooling and the cooled product is separated from the coal char.
The basic reactions involved are as follows
- 3Fe2O3 + CO = 2Fe3O4 + CO2
- Fe3O4 + CO = 3FeO + CO2
- FeO + CO = Fe + CO2
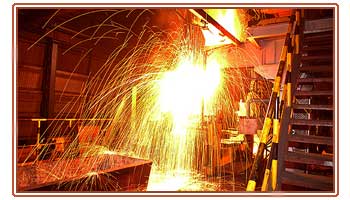
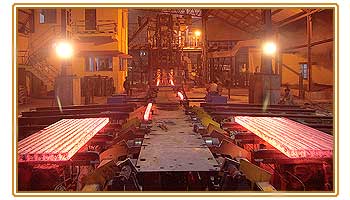
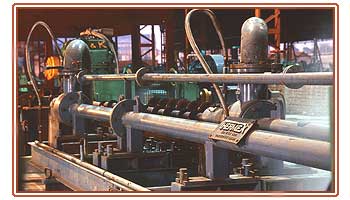
Electric Arc Furnace
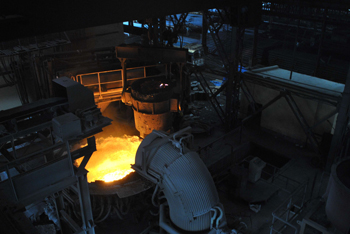
Steps involved in an arc furnace can be summarized as follows
Charging
The Charge is prepared according to the grades proposed chemistry for the targeted grade, Sponge iron and other ingredients along with lime in a close requisite ratio is charged in the arc furnace.
Melting
Melting is accomplished by injecting energy to the charge materials in the form of electrical energy through three numbers graphite electrodes. Carbon injected inside the furnace reacts with oxygen producing CO, which bubbles through the bath creating foamy slag. The excess CO reacts with oxygen, converting to CO2, again generating heat. Oxygen will react with several components present in the bath including silicon; manganese; phosphorus and sulphur. The oxides thus formed will end up in the slag. In arc furnace charged materials get melted at about 1800°C.
Once sufficient charge has been melted and enough space has been created, the second charge can be taken and the process is repeated. Once the final charge has been melted and is reached at melt stage, Temperature measurement is taken and the sample is drawn for determining the amount of oxygen to be blown during refining.
Refining
Refining means the reduction of undesirable elements in steel like sulphur, Phosphorus etc and also bringing down the carbon to required levels.
Phosphorus and sulphur which cannot be removed from Induction Furnace can be easily removed in EAF. Phosphorous is removed in the early stage of refining. Sulphur is removed as sulphides in slag and is better achieved during the reducing stage.
Aluminum, silicon, and manganese react with oxygen before carbon to form oxides which go into the slag. CO, which is produced due to the reaction of carbon with oxygen, bubbles through the bath causing the slag to foam and has many beneficial effects. The foaming also helps in bringing down nitrogen and hydrogen levels in steel. At the end of the refining stage temperature measurement is done and the sample is drawn for analysis.
De-slagging
De-slagging is the process by which the slag layer above the steel is removed from the furnace. This process is important for removing impurities from the molten material.
The furnace is tilted towards the slag door for slag removal. Phosphorus is transferred to the slag, during the early stage of the heating while the temperature is relatively low. The first de-slagging (at the beginning of refining) removes the substantial portion of the phosphorous (as P2O5) thus preventing phosphorous reversal to the metal. Typically during the refining state, the furnace may be de-slagged several times.
Tapping
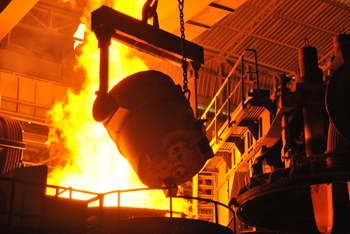
After reaching the required temperature and composition, the tap hole is opened and metal is tapped into the ladle and sent to continuous casting unit for the casting of billets, during the tapping process bulk alloys are based on the bath analysis for the desired steel grade. De-oxiders may be added to the steel to control the oxygen content, prior to further processing. This is commonly referred to as killing of steel. This is done by adding aluminum or silicon in the form of ferrosilicon or silicon manganese.
A typical construction of Arc Furnace has been shown above.
Continuous Billets Casting
Molten Steel from EAF is tapped into a laddle and taken to the continuous casting machine. Liquid steel flows out of the laddle into the tundish and then into water-cooled mold. Solidification begins in the mold. The continuous Billets coming out from the CCM is sized according to the length required.
Rolling Mill with Thermex Technology
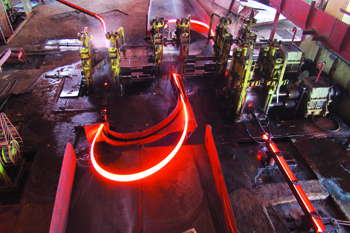
The billets manufactured are re-heated at a temp of 1200°C in the re-heating furnace and rolled into specific sections of finished material in the Rolling Mill Unit. In the case of manufacturing TMT Re-bars, from the finishing stand of the rolling Mill, the Re-Bars are guided through a specially designed propriety Thermex pipes to obtain special property ‘Thermax Process’ as explained below:
Quenching
The hot rolled bar from the finished mill stand enters into the ‘Thermex System’ and is rapidly cooled by a special water spray system. This rapid cooling hardens the surface of the TMT Re-bars to a depth optimized for each section, forming a martensitic rim while the core remains hot and & Austenitic. This rapid cooling is called quenching.
Self Tempering
After Re-bars leave the quenching box, the core remains hot compared to the surface allowing heat to flow from the core to the surface causing Tempering of the outer Martensite layer thus forming a structure called ‘Tempered Martensite’.
Atmospheric Cooling
This takes place on the cooling bed, where the Austenitic core is transformed into ductile Ferrite-Perlite structure. Thus the final structure consist of stronger outer layer (Tempered Mastensite) with ductile core (Ferrite-Pearlite). This process increases the tensile strength of the material while keeping high ductile and weldability. Best TMT Bar Manufacturing Plants India – This whole process is a patented technology from HSE, Germany under the brand name of ‘Thermex‘.